SMT използва конвенционален анализ на заваръчната кухина с въздушна паста за запояване и решение (2023 Essence Edition), вие го заслужавате!
1 Въведение

В модула на печатната платка първо се отпечатва спояваща паста върху подложката за запояване на платката и след това се закрепват различни електронни компоненти. Накрая, след пещта за повторно оформяне, калаените перли в спояващата паста се разтопяват и всички видове електронни компоненти и подложката за запояване на печатната платка се заваряват заедно, за да се реализира сглобяването на електрически подмодули. технологията за повърхностно монтиране (sMT) се използва все по-често в опаковъчни продукти с висока плътност, като пакет на системно ниво (siP), устройства с ballgridarray (BGA) и захранващ гол чип, квадратен плосък пакет без щифтове (quad aatNo-lead, наричан QFN ) устройство.
Поради характеристиките на процеса на заваряване с паста за запояване и материалите, след заваряване с препълване на тези устройства с голяма повърхност за запояване ще има дупки в зоната на заваряване на спойка, което ще повлияе на електрическите свойства, термичните свойства и механичните свойства на продукта. дори да доведе до повреда на продукта, следователно, за да се подобри спояващата паста, заваръчната кухина се превърна в процес и технически проблем, който трябва да бъде разрешен, някои изследователи са анализирали и проучили причините за BGA кухина за заваряване на топка за запояване и предоставени решения за подобрение, процес на заваряване с конвенционален процес на заваряване с паста за запояване, площ на заваряване на QFN, по-голяма от 10 mm2, или площ на заваряване, по-голяма от 6 mm2, липсва решение за чист чип.
Използвайте заваряване с предварително формовано запояване и заваряване във вакуумна пещ с обратен хладник, за да подобрите заваръчния отвор. Сглобяемата спойка изисква специално оборудване за насочване на потока. Например, чипът е изместен и наклонен сериозно, след като чипът е поставен директно върху предварително изработената спойка. Ако чипът за монтиране на флюс е преформатиран и след това точков, процесът се увеличава с две преформатиране и цената на сглобяемите спойки и флюсов материал е много по-висока от спояващата паста.
Оборудването за вакуумен обратен хладник е по-скъпо, капацитетът на вакуума на независимата вакуумна камера е много нисък, производителността на разходите не е висока и проблемът с пръскането на калай е сериозен, което е важен фактор при прилагането на висока плътност и малка стъпка продукти. В тази статия, въз основа на конвенционалния процес на заваряване с преплавяне на спояваща паста, е разработен и въведен нов вторичен процес на заваряване с преплавяне, за да се подобри заваръчната кухина и да се решат проблемите със залепването и напукването на пластмасовото уплътнение, причинени от заваръчната кухина.
2 Кухина за заваряване с печатане на спояваща паста и механизъм за производство
2.1 Заваръчна кухина
След заваряване с преплавяне продуктът беше тестван с рентгенови лъчи. Установено е, че дупките в зоната на заваряване с по-светъл цвят се дължат на недостатъчно спойка в заваръчния слой, както е показано на фигура 1
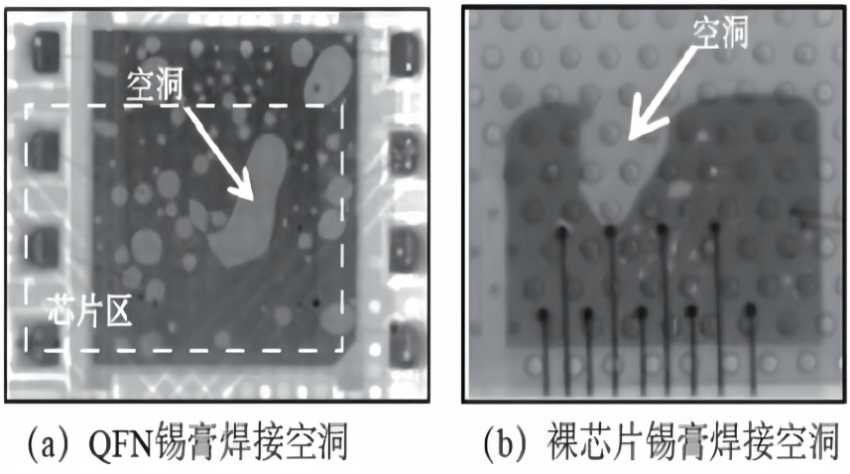
Рентгеново откриване на мехурчеста дупка
2.2 Механизъм на образуване на заваръчна кухина
Като вземем за пример спояваща паста sAC305, основният състав и функция са показани в таблица 1. Флюсът и калаените перли са свързани заедно във формата на паста. Тегловното съотношение на калаения припой към флюса е около 9:1, а обемното съотношение е около 1:1.
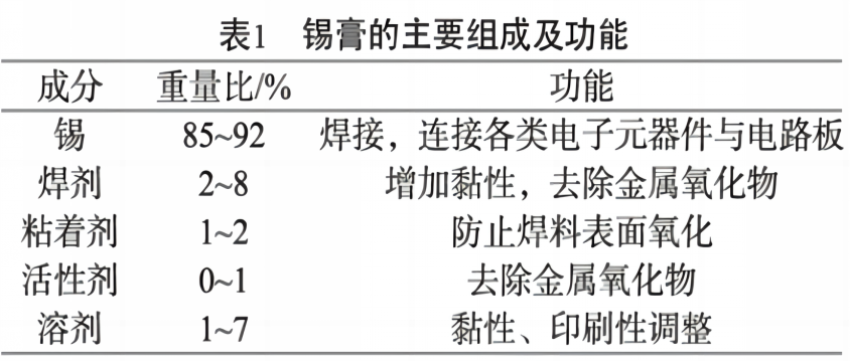
След като пастата за запояване бъде отпечатана и монтирана с различни електронни компоненти, пастата за запояване ще претърпи четири етапа на предварително загряване, активиране, обратен хладник и охлаждане, когато премине през рефлуксната пещ. Състоянието на спояващата паста също е различно при различни температури в различните етапи, както е показано на фигура 2.
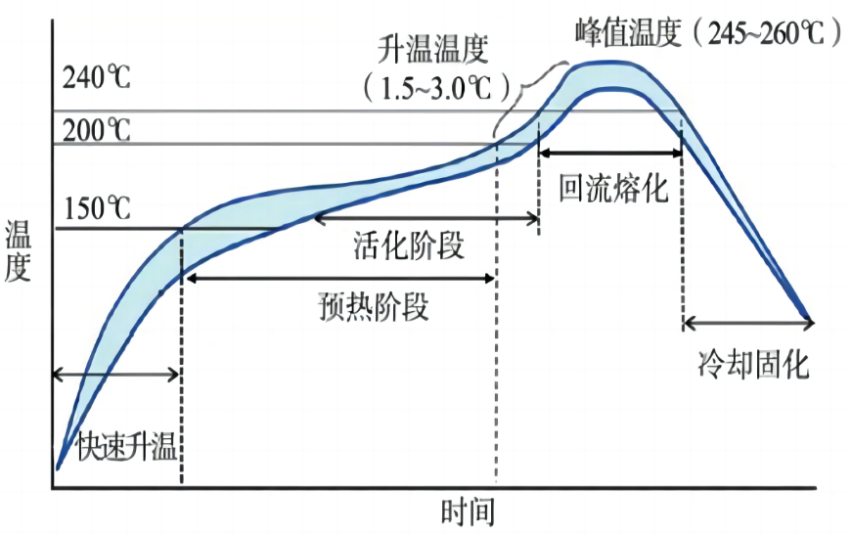
Профилен справочник за всяка област на запояване с преплавяне
В етапа на предварително загряване и активиране, летливите компоненти във флюса в спояващата паста ще се изпарят в газ при нагряване. В същото време ще се образуват газове, когато оксидът на повърхността на заваръчния слой бъде отстранен. Някои от тези газове ще се изпарят и ще напуснат пастата за запояване, а перлите за спояване ще бъдат плътно кондензирани поради изпаряването на флюса. В етапа на обратен хладник оставащият флюс в спояващата паста ще се изпари бързо, калаените перли ще се стопят, малко количество летлив газ и по-голямата част от въздуха между калаените перли няма да се разпръснат навреме и остатъкът в разтопен калай и под напрежението на разтопения калай са сандвич структура на хамбургер и се улавят от подложката за запояване на печатната платка и електронните компоненти, и газът, обвит в течния калай, е труден за излизане само от насочената нагоре плаваемост. Горното време на топене е много кратко. Когато разтопеният калай се охлади и стане твърд калай, в заваръчния слой се появяват пори и се образуват отвори за спояване, както е показано на Фигура 3.
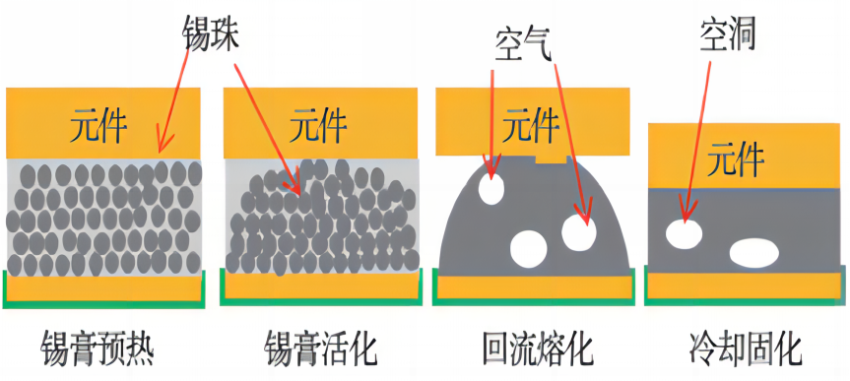
Схематична диаграма на празнина, генерирана от заваряване с преплавяне на спояваща паста
Основната причина за заваръчната кухина е, че въздухът или летливият газ, обвит в спояващата паста след топене, не се изхвърля напълно. Влияещите фактори включват материал на паста за запояване, форма на печат на паста за запояване, количество за печат на паста за запояване, температура на обратен хладник, време на обратен хладник, размер на заваряване, структура и т.н.
3. Проверка на факторите на влияние върху отворите за заваряване чрез претопяване при печатане на спояваща паста
Тестовете QFN и голи чипове бяха използвани, за да се потвърдят основните причини за кухини при заваряване с преплавяне и за намиране на начини за подобряване на кухините при заваряване с преплавяне, отпечатани от спояваща паста. Профилът на заваръчния продукт за заваряване на QFN и голи чипове с претопена паста за запояване е показан на фигура 4, размерът на заваръчната повърхност на QFN е 4,4 mm x 4,1 mm, заваръчната повърхност е калайдисан слой (100% чист калай); Размерът на заваряване на голия чип е 3,0 mmx2,3 mm, заваръчният слой е разпръснат никел-ванадиев биметален слой, а повърхностният слой е ванадий. Заваръчната подложка на субстрата беше без електролитно потапяне в никел-паладиево злато, а дебелината беше 0,4 μm/0,06 μm/0,04 μm. Използва се паста за запояване SAC305, оборудването за печат на паста за запояване е DEK Horizon APix, оборудването за рефлуксна пещ е BTUPyramax150N, а рентгеновото оборудване е DAGExD7500VR.
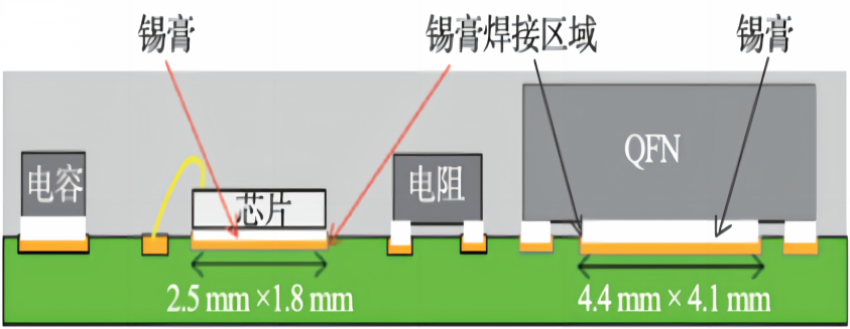
Чертежи за заваряване на QFN и голи чипове
За да се улесни сравнението на резултатите от изпитването, беше извършено заваряване с преплавяне при условията в таблица 2.
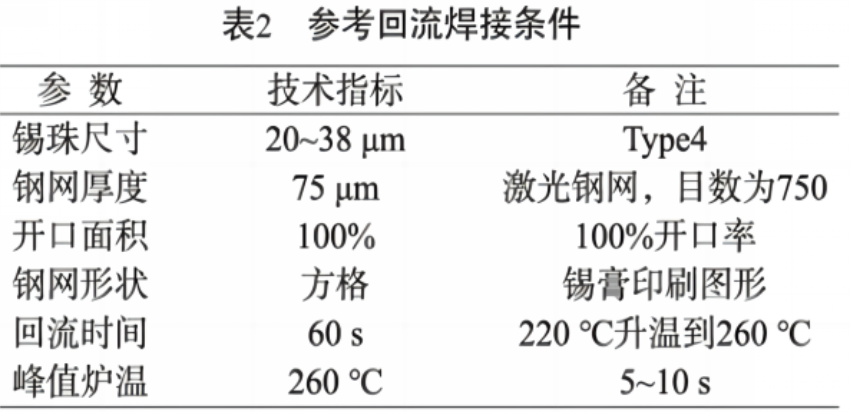
Таблица на условията на заваряване чрез препълване
След завършване на повърхностния монтаж и заваряването с преплавяне, заваръчният слой беше открит с рентгенови лъчи и беше установено, че има големи дупки в заваръчния слой в долната част на QFN и голия чип, както е показано на Фигура 5.
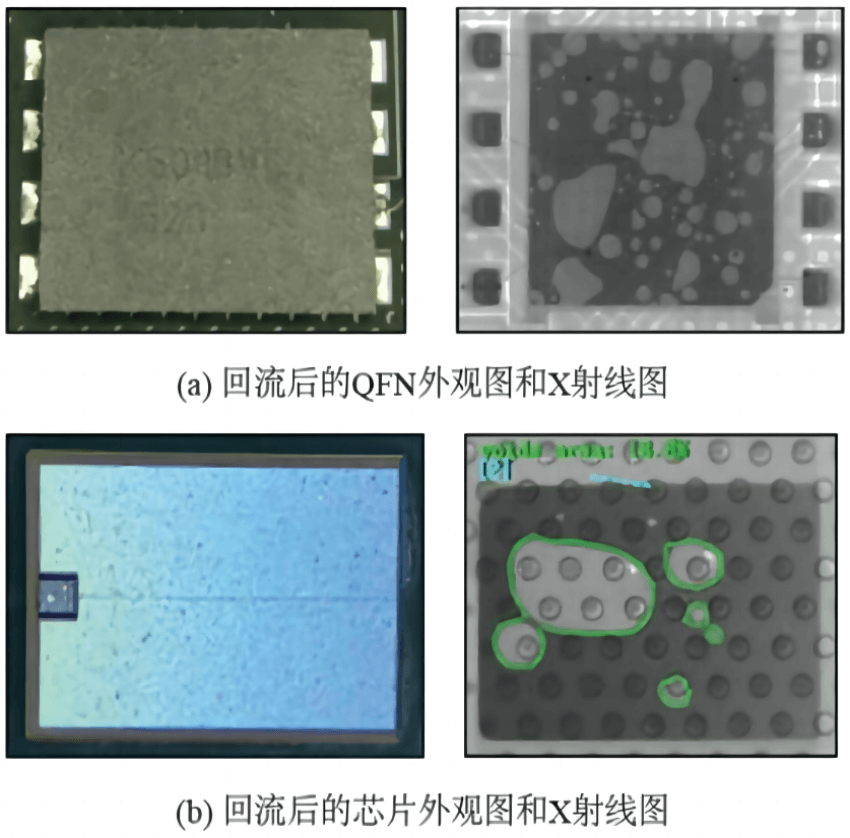
QFN и холограма на чип (рентген)
Тъй като размерът на калаените зърна, дебелината на стоманената мрежа, степента на отваряне на площта, формата на стоманената мрежа, времето на обратен хладник и пиковата температура на пещта ще повлияят на кухините при заваряване с преплавяне, има много влияещи фактори, които ще бъдат директно проверени от теста на DOE и броя на експерименталните групите ще бъдат твърде големи. Необходимо е бързо да се скринират и определят основните влияещи фактори чрез корелационен сравнителен тест и след това допълнително да се оптимизират основните влияещи фактори чрез DOE.
3.1 Размери на отворите за запояване и калаените перли от спояваща паста
При тип 3 (размер на перлите 25-45 μm) SAC305 тест за спояваща паста, другите условия остават непроменени. След преформатиране дупките в слоя спойка се измерват и се сравняват с паста тип 4. Установено е, че дупките в слоя за запояване не се различават значително между двата вида паста за запояване, което показва, че пастата за запояване с различен размер на перлите няма очевидно влияние върху дупките в слоя за запояване, което не е влияещ фактор, както е показано на фиг. 6 Както е показано.
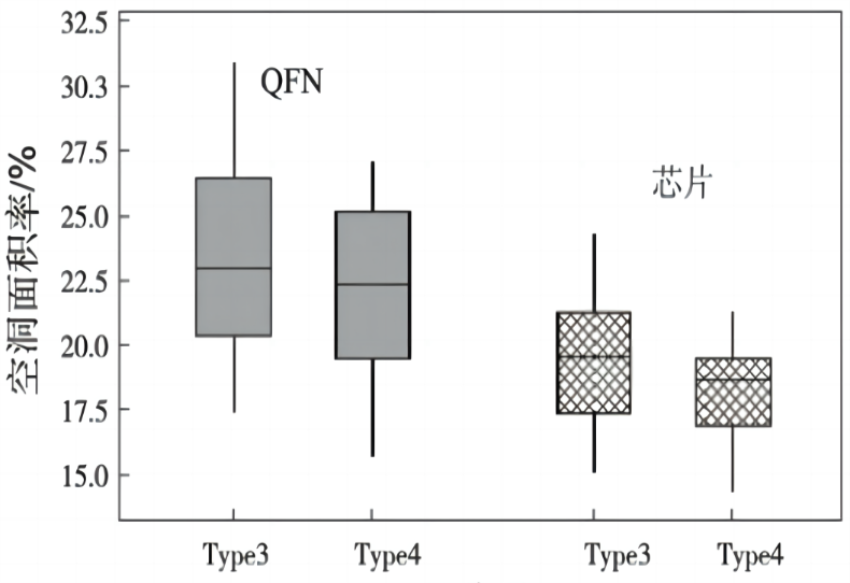
Сравнение на дупки от метален калаен прах с различни размери на частиците
3.2 Дебелина на заваръчната кухина и отпечатана стоманена мрежа
След префлояване площта на кухината на заварения слой беше измерена с отпечатана стоманена мрежа с дебелина 50 μm, 100 μm и 125 μm, а други условия останаха непроменени. Установено е, че ефектът от различната дебелина на стоманената мрежа (спояваща паста) върху QFN е сравнен с този на отпечатаната стоманена мрежа с дебелина 75 μm С увеличаване на дебелината на стоманената мрежа, площта на кухината постепенно намалява бавно. След достигане на определена дебелина (100 μm), площта на кухината ще се обърне и ще започне да се увеличава с увеличаването на дебелината на стоманената мрежа, както е показано на Фигура 7.
Това показва, че когато количеството спояваща паста се увеличи, течният калай с обратен хладник се покрива от чипа и изходът на остатъчния въздух е тесен само от четири страни. Когато количеството спояваща паста се промени, изходът на остатъчния въздух също се увеличава и мигновеният изблик на въздух, обвит в течен калай или летлив газ, изпускащ течен калай, ще доведе до пръскане на течен калай около QFN и чипа.
Тестът установи, че с увеличаването на дебелината на стоманената мрежа спукването на мехурчета, причинено от изтичане на въздух или летлив газ, също ще се увеличи и вероятността от пръскане на калай около QFN и чипа също ще се увеличи съответно.
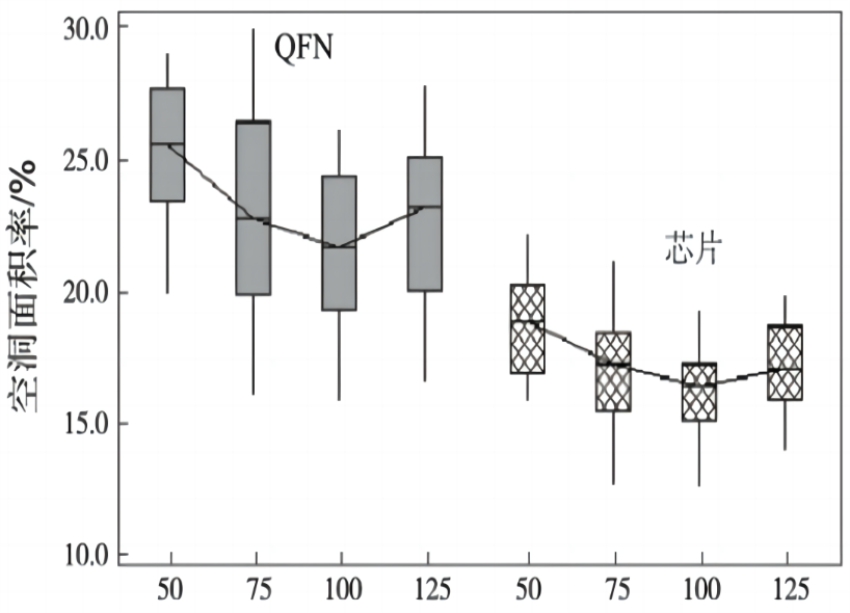
Сравнение на отвори в стоманена мрежа с различна дебелина
3.3 Съотношение на площта на заваръчната кухина и отвора на стоманената мрежа
Отпечатаната стоманена мрежа със степен на отваряне от 100%, 90% и 80% беше тествана, а другите условия останаха непроменени. След преформатиране, площта на кухината на заварения слой беше измерена и сравнена с отпечатаната стоманена мрежа със 100% скорост на отваряне. Установено е, че няма значителна разлика в кухината на заварения слой при условия на скорост на отваряне от 100% и 90% 80%, както е показано на фигура 8.
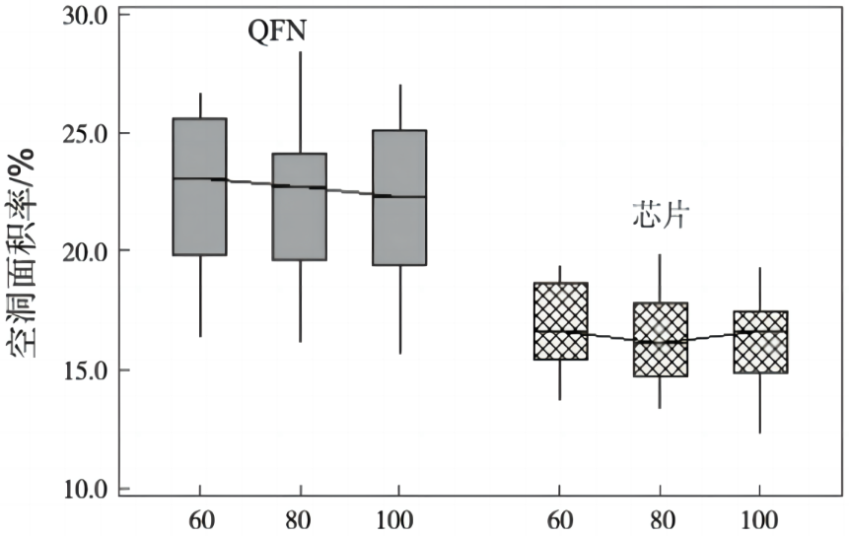
Сравнение на кухини на различни отвори на различни стоманени мрежи
3.4 Заварена кухина и форма на отпечатана стоманена мрежа
С теста за форма на печат на паста за запояване на лента b и наклонена решетка c, другите условия остават непроменени. След преформатиране площта на кухината на заваръчния слой се измерва и се сравнява с печатната форма на решетка a. Установено е, че няма значителна разлика в кухината на заваръчния слой при условията на решетка, лента и наклонена решетка, както е показано на фигура 9.
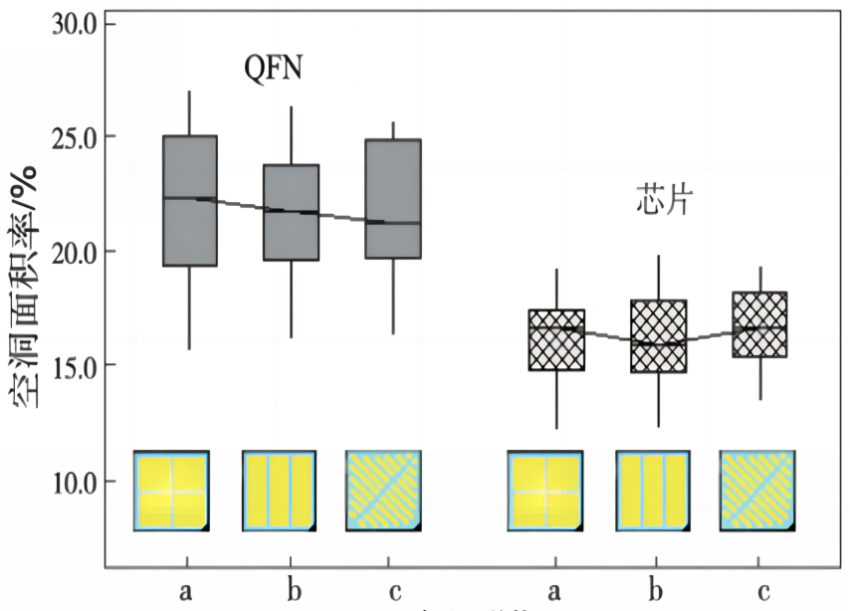
Сравнение на отворите при различни режими на отваряне на стоманена мрежа
3.5 Заваръчна кухина и време на обратен хладник
След продължително време на обратен хладник (70 s, 80 s, 90 s) тест, други условия остават непроменени, дупката в заваръчния слой беше измерена след обратен хладник и в сравнение с времето на обратен хладник от 60 s беше установено, че с увеличаването на време на обратен хладник, площта на отвора за заваряване намалява, но амплитудата на намаляване постепенно намалява с увеличаването на времето, както е показано на фигура 10. Това показва, че в случая на недостатъчно време на обратен хладник, увеличаването на времето на обратен хладник е благоприятно за пълното преливане на въздух, обвит в разтопен течен калай, но след като времето на обратен хладник се увеличи до определено време, въздухът, обвит в течен калай, е трудно да прелее отново. Времето на обратен хладник е един от факторите, влияещи върху заваръчната кухина.
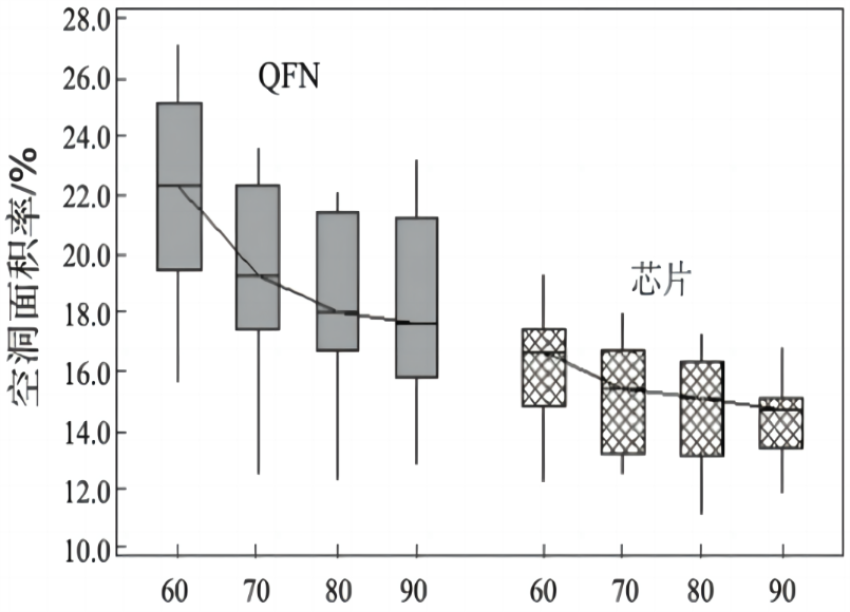
Празно сравнение на различни дължини на времето на рефлукс
3.6 Заваръчна кухина и пикова температура на пещта
При 240 ℃ и 250 ℃ тест за пикова температура на пещта и други условия непроменени, площта на кухината на заварения слой беше измерена след претопяване и в сравнение с 260 ℃ пикова температура на пещта беше установено, че при различни условия на пикова температура на пещта, кухината на завареният слой на QFN и чипа не се промени значително, както е показано на фигура 11. Това показва, че различната пикова температура на пещта няма очевиден ефект върху QFN и дупката в заваръчния слой на чипа, което не е влияещ фактор.
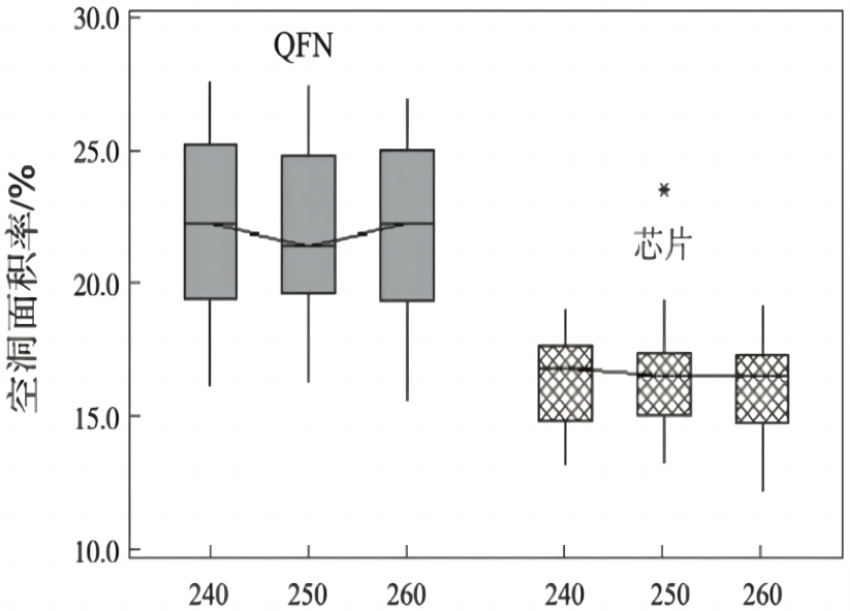
Безсмислено сравнение на различни пикови температури
Горните тестове показват, че значимите фактори, влияещи върху кухината на заваръчния слой на QFN и чипа, са времето на обратен хладник и дебелината на стоманената мрежа.
4 Подобряване на кухината за печатане на спояваща паста
4.1DOE тест за подобряване на заваръчната кухина
Дупката в заваръчния слой на QFN и чипа беше подобрена чрез намиране на оптималната стойност на основните влияещи фактори (време на обратен хладник и дебелина на стоманената мрежа). Спояващата паста беше SAC305 тип 4, формата на стоманената мрежа беше тип решетка (100% степен на отваряне), пиковата температура на пещта беше 260 ℃, а другите условия на изпитване бяха същите като тези на оборудването за изпитване. Тестът на DOE и резултатите са показани в таблица 3. Влиянието на дебелината на стоманената мрежа и времето на обратен хладник върху QFN и отворите за заваряване на чипове са показани на фигура 12. Чрез анализа на взаимодействието на основните влияещи фактори е установено, че при използване на дебелина на стоманената мрежа от 100 μm и 80 s време на обратен хладник може значително да намали заваръчната кухина на QFN и чипа. Степента на заваръчна кухина на QFN е намалена от максималните 27,8% на 16,1%, а скоростта на заваръчна кухина на чипа е намалена от максималните 20,5% на 14,5%.
При теста бяха произведени 1000 продукта при оптимални условия (100 μm дебелина на стоманената мрежа, 80 s време на обратен хладник) и скоростта на заваръчната кухина от 100 QFN и чипът бяха измерени на случаен принцип. Средният процент на заваръчна кухина на QFN беше 16,4%, а средният процент на заваръчна кухина на чипа беше 14,7%. Степента на заваръчна кухина на чипа и чипа очевидно са намалени.
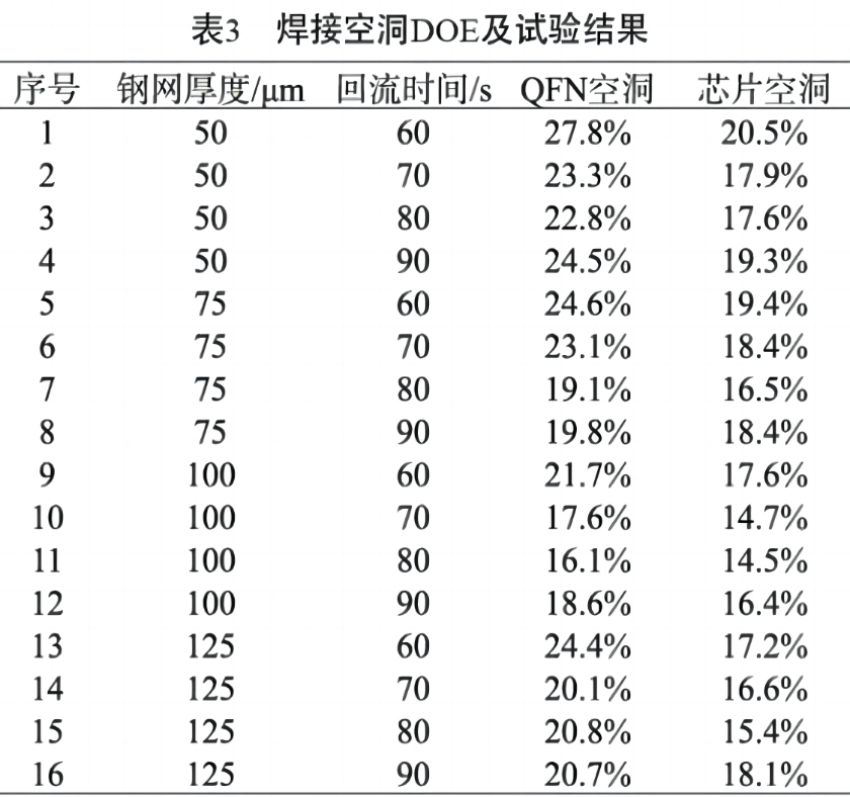
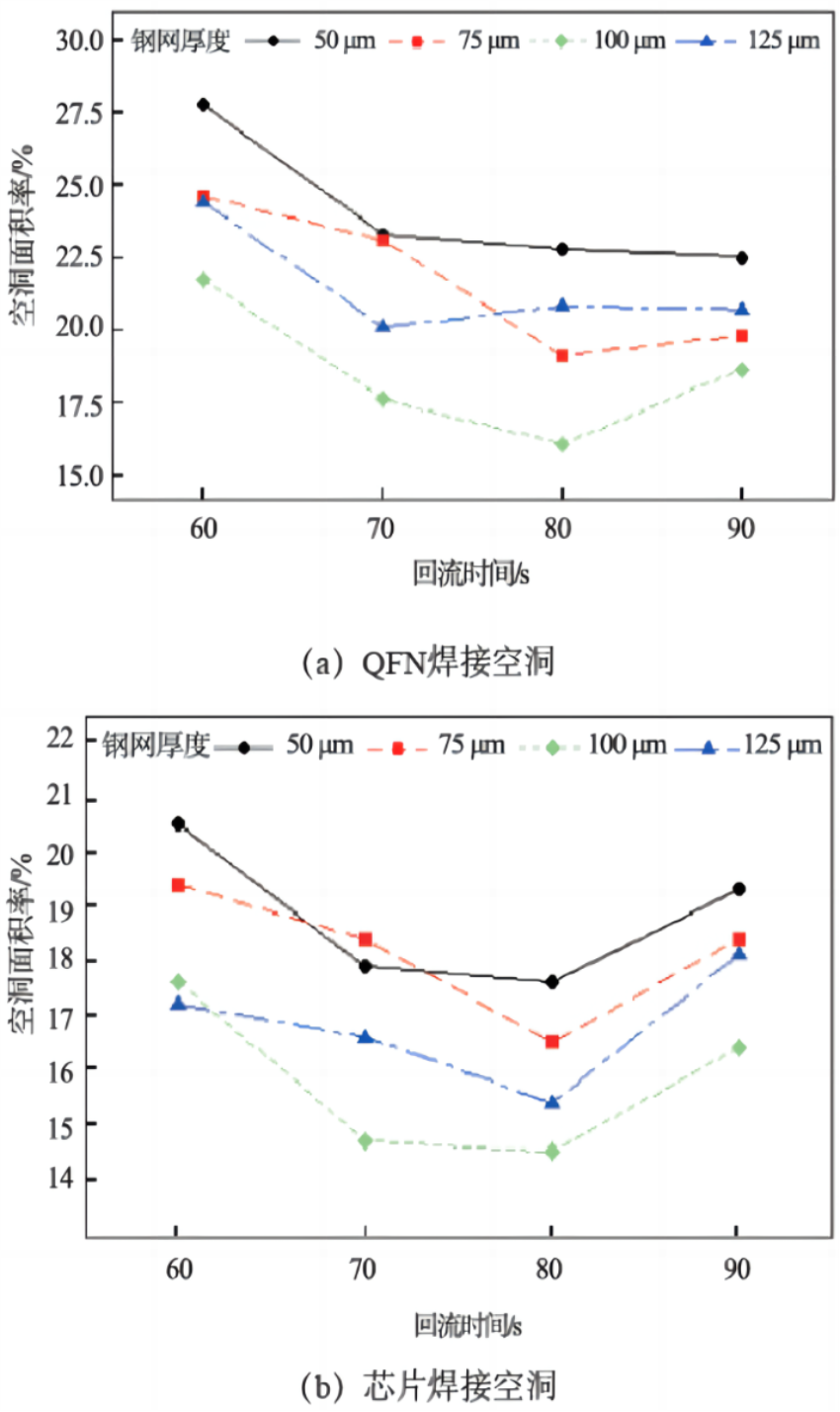
4.2 Новият процес подобрява заваръчната кухина
Действителната производствена ситуация и тестът показват, че когато площта на заваръчната кухина в долната част на чипа е по-малка от 10%, проблемът с напукването на позицията на кухината на чипа няма да възникне по време на залепването и формоването на оловото. Параметрите на процеса, оптимизирани от DOE, не могат да отговорят на изискванията за анализиране и решаване на дупките при конвенционалното заваряване с преплавяне на спояваща паста и площта на заваръчната кухина на чипа трябва да бъде допълнително намалена.
Тъй като чипът, покрит върху спойката, предотвратява изтичането на газа в спойката, скоростта на дупките в долната част на чипа се намалява допълнително чрез елиминиране или намаляване на газа, покрит с спойка. Възприет е нов процес на заваряване с преплавяне с две отпечатвания на спояваща паста: едно отпечатване на спояваща паста, едно преплавяне, което не покрива QFN и гол чип, изпускащ газа в спойката; Специфичният процес на отпечатване на вторична спояваща паста, пластир и вторичен обратен хладник е показан на фигура 13.
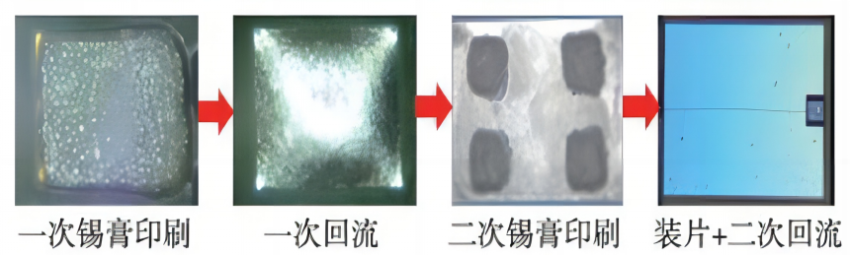
Когато спояващата паста с дебелина 75 μm се отпечатва за първи път, по-голямата част от газа в спойката без капак на чипа излиза от повърхността и дебелината след обратен хладник е около 50 μm. След завършване на първичния обратен хладник, върху повърхността на охладения втвърден припой се отпечатват малки квадратчета (за да се намали количеството спояваща паста, да се намали количеството на разливането на газ, да се намалят или елиминират пръските от спойка) и спояващата паста с дебелина от 50 μm (горните резултати от теста показват, че 100 μm е най-добрият, така че дебелината на вторичния печат е 100 μm.50 μm=50 μm), след това инсталирайте чипа и след това се върнете през 80 s. Почти няма дупка в спойката след първото отпечатване и преформатиране, а спояващата паста при второто отпечатване е малка, а отворът за заваряване е малък, както е показано на фигура 14.
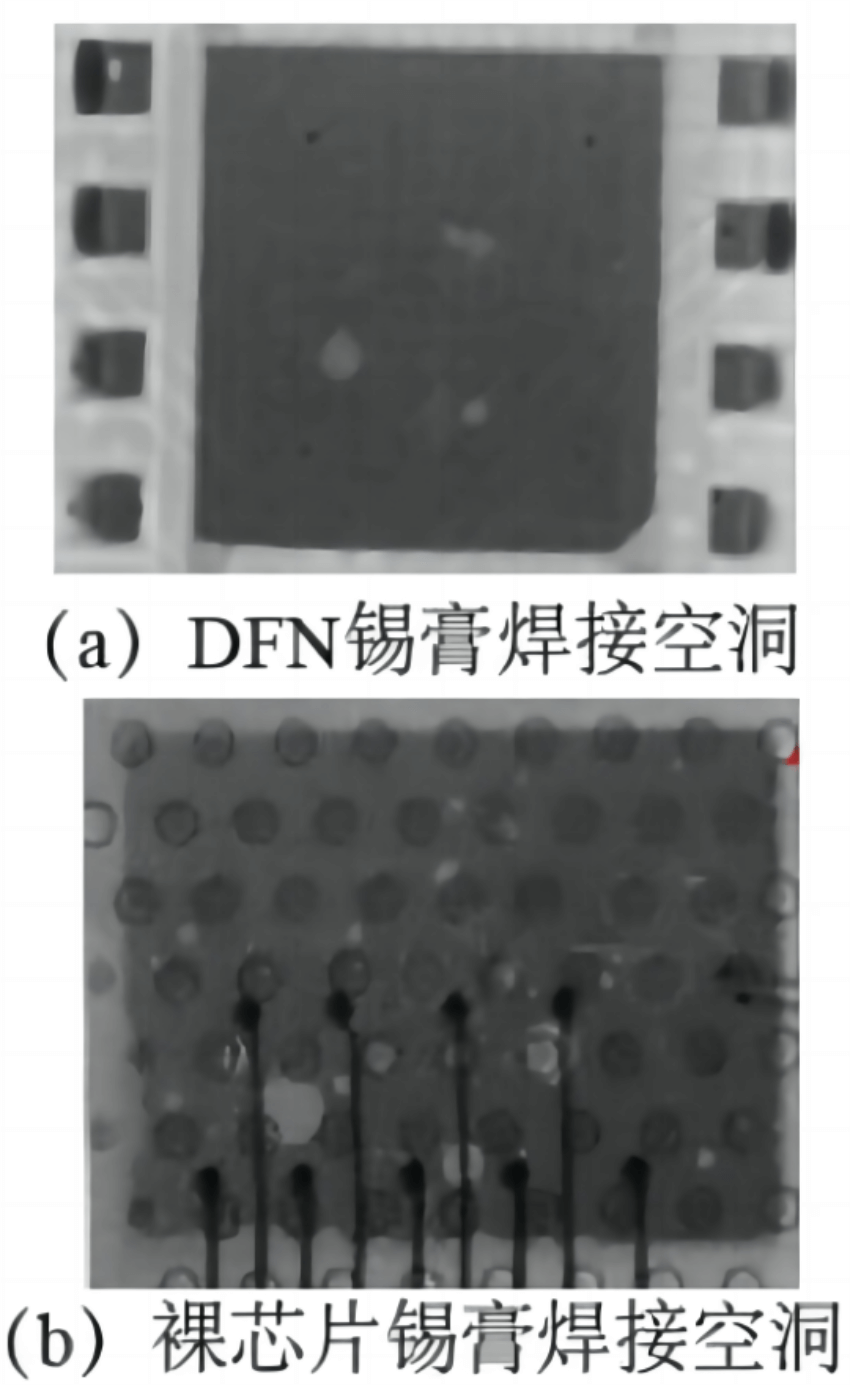
След две разпечатки на спояваща паста, кух чертеж
4.3 Проверка на ефекта на заваръчната кухина
Производство на 2000 продукта (дебелината на първата печатаща стоманена мрежа е 75 μm, дебелината на втората печатаща стоманена мрежа е 50 μm), други условия непроменени, произволно измерване от 500 QFN и скорост на кухина за заваряване на чипове, установи, че новият процес след първия обратен хладник без кухина, след втория обратен хладник QFN Максималната скорост на заваряване на кухината е 4,8%, а максималната степен на заваръчна кухина на чипа е 4,1%. В сравнение с оригиналния процес на заваряване с печатане с една паста и оптимизирания от DOE процес, заваръчната кухина е значително намалена, както е показано на Фигура 15. След функционални тестове на всички продукти не са открити пукнатини.
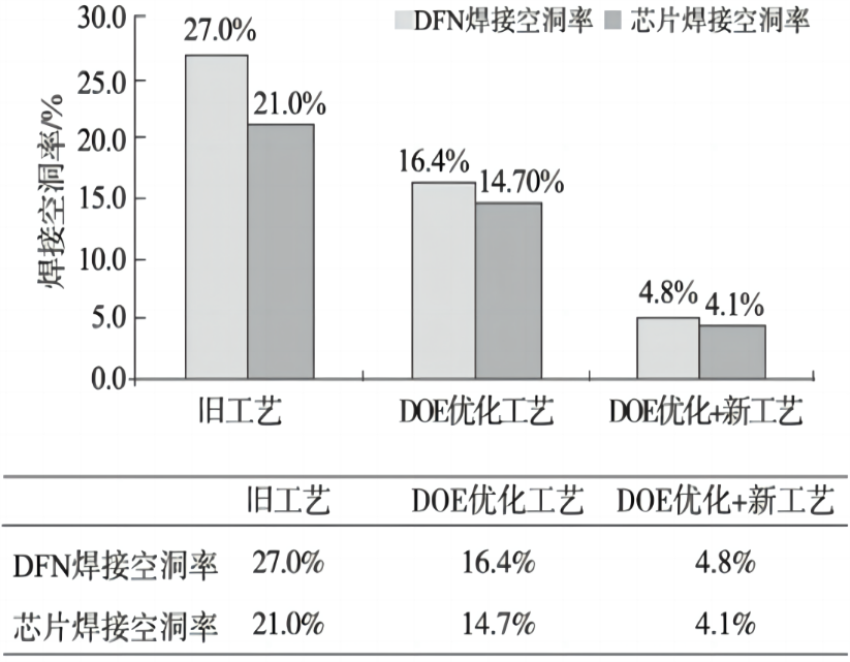
5 Резюме
Оптимизирането на количеството отпечатана паста за запояване и времето на обратен хладник може да намали площта на заваръчната кухина, но скоростта на заваръчната кухина все още е голяма. Използването на две техники за заваряване с печатане на спояваща паста може ефективно и да увеличи максимално скоростта на заваръчната кухина. Зоната на заваряване на чистия чип на веригата QFN може да бъде съответно 4,4 mm x 4,1 mm и 3,0 mm x 2,3 mm при масово производство Скоростта на кухина при заваряване с преплавяне се контролира под 5%, което подобрява качеството и надеждността на заваряването с преплавяне. Изследването в тази статия предоставя важна справка за подобряване на проблема със заваръчната кухина на заваръчна повърхност с голяма площ.